A Comprehensive Guide to the Sorts Of Ceramic Coating on the Market
Ceramic coverings have arised as a pivotal solution throughout numerous sectors due to their one-of-a-kind buildings and applications. As we check out the distinctive features and applications of these coverings, the implications for efficiency and durability become significantly noticeable, raising questions about which type might ideal fit your requirements.
Understanding Ceramic Coatings
Ceramic coverings are innovative safety services that have actually gained popularity in numerous sectors, specifically in automotive and aerospace applications. These finishes include a liquid polymer that, when treated, forms a resilient, hydrophobic layer on the surface area of the substrate. This layer provides enhanced resistance to environmental pollutants, UV radiation, and chemical exposure, thus extending the life and aesthetic appeal of the underlying product.
The basic element of ceramic finishings is silica, which contributes to their solidity and resilience. The application process commonly includes surface prep work, application of the finish, and treating, which can be achieved via warm or UV light. As soon as cured, ceramic coatings exhibit extraordinary bonding buildings, enabling them to adhere highly to a variety of surface areas, including metals, plastics, and glass.
In addition to their safety attributes, ceramic finishings also use ease of upkeep. Their hydrophobic nature reduces the adherence of dust and grime, making cleansing less complex and less constant. In general, the fostering of ceramic coverings stands for a significant innovation in surface security modern technology, offering both useful and aesthetic advantages throughout multiple markets.
Kinds Of Ceramic Coatings
Different kinds of ceramic coverings are readily available, each designed to satisfy certain efficiency requirements and applications - ceramic coating sarasota. The most typical kinds consist of:
Silica-based Coatings: These coverings mostly are composed of silicon dioxide and are known for their sturdiness and chemical resistance. They are extensively used in automobile and industrial applications.
Titanium Dioxide Coatings: Distinguished for their photocatalytic buildings, titanium dioxide finishings are usually applied in environments where self-cleaning and antifungal residential or commercial properties are desirable, such as in structure materials and auto coatings.
Zirconia Coatings: Defined by their high-temperature security and thermal resistance, zirconia finishings are made use of in applications such as wind turbine engines and high-performance vehicle components.
Alumina Coatings: Exhibiting outstanding solidity and thermal security, alumina coatings are regularly utilized in wear-resistant applications, including reducing tools and industrial equipment. - Car Detailing
Hybrid Coatings: Incorporating the buildings of different materials, crossbreed coverings provide boosted performance features, making them ideal for one-of-a-kind and demanding applications.
Each sort of ceramic coating offers unique purposes, permitting customers to choose the most ideal option based upon certain environmental conditions and performance demands.
Benefits of Ceramic Coatings
Ceramic coatings, in particular, offer many advantages that make them increasingly popular among makers and consumers alike. These finishes are immune to scrapes, chemicals, best site and UV rays, ensuring that the underlying surface remains protected over time.
In enhancement to resilience, ceramic finishes give excellent hydrophobic buildings, permitting easy cleaning and upkeep. This water-repellent nature minimizes the adherence of dirt, grime, and various other impurities, which can lengthen the visual allure and capability of the surface area. Ceramic finishings can substantially improve thermal resistance, making them suitable for applications that sustain high temperature levels.

Application Refine
When applying ceramic coatings, a precise strategy is vital to attain optimal results. A tidy surface area guarantees correct adhesion of the finish.
When the surface is prepped, the next step is to use the ceramic layer. This can be done making use of an applicator pad or a microfiber cloth, ensuring also insurance coverage. It is important to function in small sections to maintain control and avoid early healing. The coating ought to be applied in slim layers, as thicker applications can bring about irregular finishes.
After application, the finishing needs a specific healing time, commonly ranging from a few hours to a complete day, depending on the product. Following these actions carefully will take full advantage of the efficiency and longevity of the ceramic finishing, giving a durable safety layer for the surface.
Upkeep and Longevity
To make certain the longevity and performance of a ceramic coating, routine upkeep is essential. Ceramic finishes, recognized for their sturdiness and safety top qualities, require particular treatment regimens to optimize their lifespan and performance.
Along with routine cleaning, routine evaluations are vital. Seek signs of wear or damage, such as hydrophobic properties decreasing or surface flaws. If needed, a light gloss might be used to renew the coating without stripping it away.
Furthermore, the application of a booster spray can improve the finish's hydrophobic results and recover its gloss. This is specifically valuable for coatings that have remained in usage for an extended duration. Inevitably, by adhering to these maintenance practices, one can substantially expand the life of a ceramic layer, ensuring that it remains to give optimum security against environmental factors and my blog maintain the visual charm of the car.
Final thought
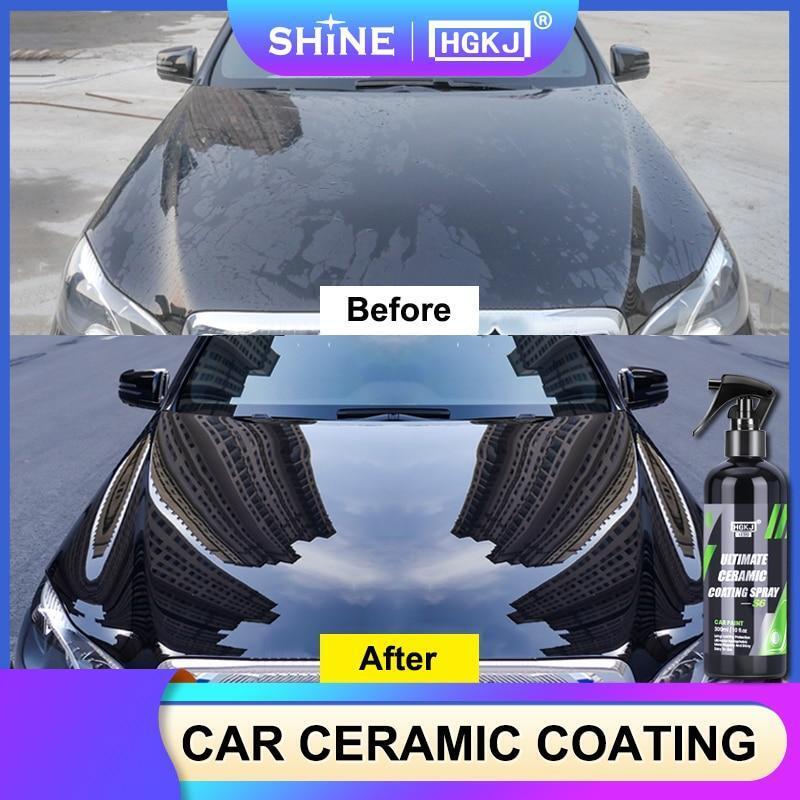